Jパネルの製造工程
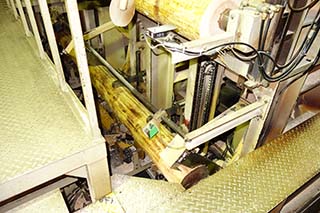
1 丸太玉切り
丸太を半分の長さに切ることで歩留まりを向上させる。
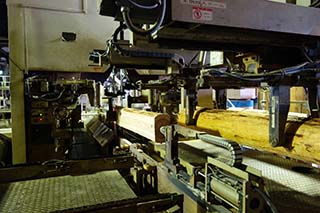
2 ツインバンドソーによる製材
サイドローラーを使って厚みむらをなくし、CCDカメラを利用して無駄なく材料を使っている。
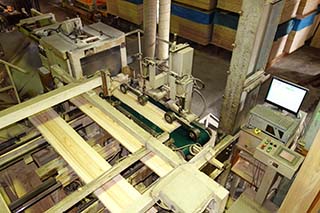
3 精密エッジャーによる耳スリ
画像処理データを利用して最大の板幅に加工することによって歩留まりを向上させる。
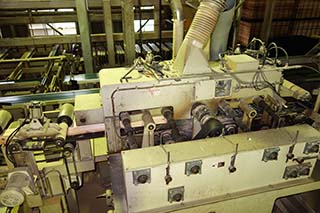
4 上下ギャングリッパ-による芯材再割
刃幅を小さくして歩留まりを高めるために径の小さい丸鋸を上下に搭載している。
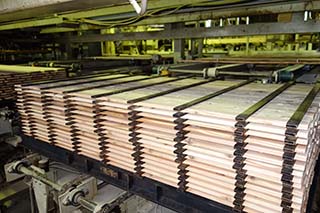
5 自動桟積み
辺材と芯材別に積み込み幅が同じようになるように其々板幅を計測し、85段、約2mの高さに自動で桟積みする。
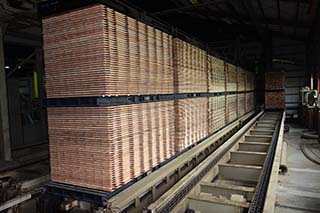
6 コンベア搬送
1つの山に1.6トンの鋼鉄製錘を自動積載し、乾燥機までコンベアによって搬送する。
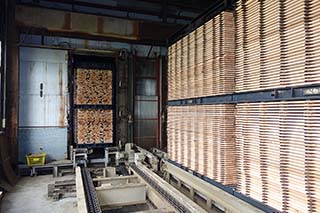
7 過熱蒸気式乾燥
過熱蒸気を使ったオリジナル乾燥機によって約30時間で含水率5%以下に乾燥させる。
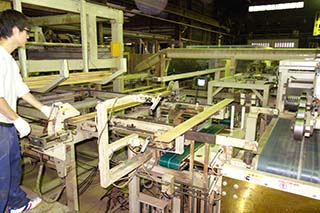
8 自動桟バラシと目視によるラミナ選別
木表・木裏や色合いは目視によって選別し品質向上と付加価値向上を兼ねている。
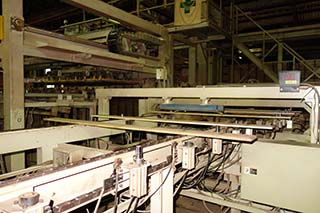
9 含水率チェック
全てのラミナは内部含水率計で自動計測し厳しく管理されている。
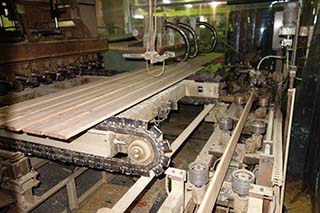
10 全自動追い継ぎ巾ハギプレス
プレス圧力は7kg/㎠で約2分間のプレスを行う。追い継ぎするので材料が無駄にならない。
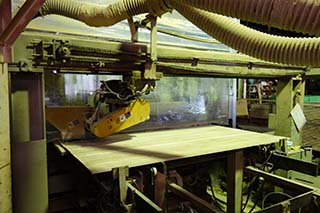
11 自動裁断
巾ハギされた元板を必要幅に自動裁断する。
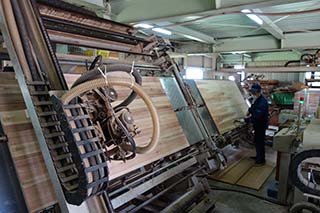
12 抜け節補修作業
作業者が目視でプロットした部分を指示された大きさ(大、小)で自動穴あけし、作業者が色合い等確認しながら埋め木する。
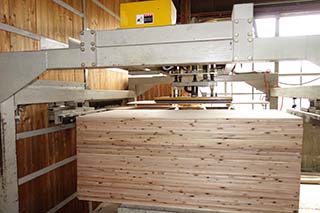
13 両面プレナー加工
大型の上下面プレナーで単板の両面を鉋加工する。接着面と化粧面になるため慎重に加工は行われる。
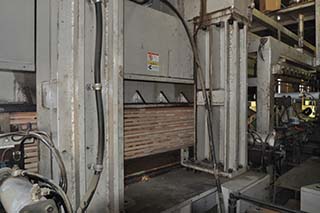
14 自動積層と140tプレス加工
単板の上面吸着搬送によって下面にむらなく接着剤を自動塗布し、堆積時間内に一定の枚数に達すると140tプレス機によって約30分の圧締加工を行う。
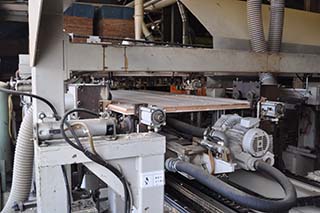
15 外周成形加工
3層に積層された元板の外周を時間を十分にかけて加工するために高精度の直角性能が生まれる。